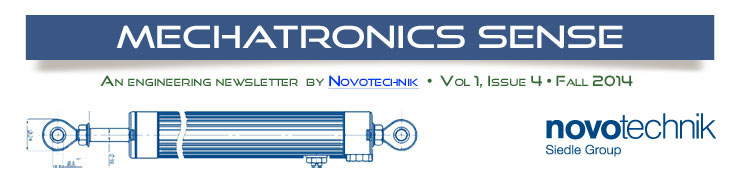 |
This issue’s articles: World's 1st 3-D Printed Car • Touchless Sensors Moving Viewing Cubes •
Power From Ocean Waves • Determining Sensor Accuracy You Need • To view newsletter as webpage click here. |
|
|
 |
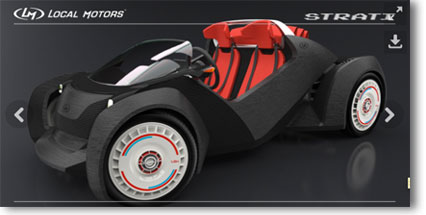
The world’s first 3-D printed car the Strati is manufactured by Local Motors, and was printed at the 2014 IMTS show in Chicago, Illinois. It was printed in 44 hours and has a top speed of approximately 50 mph. Strati is a battery-powered vehicle with a carbon fiber reinforced ABS plastic body with 212 layers. It has a 62 mile range and its motor produces 42 lb-ft of torque.
Source: Local Motors, Inc.
|
|
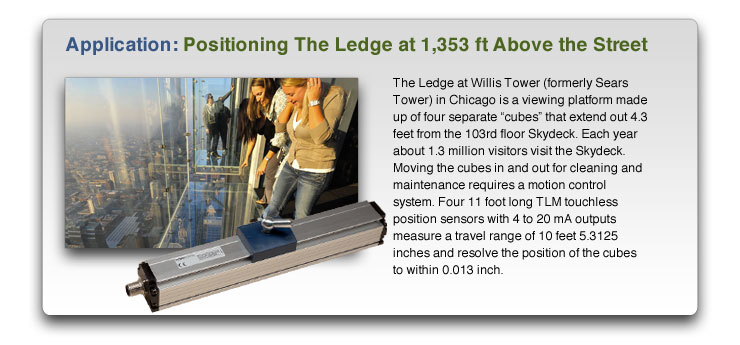 |
 |
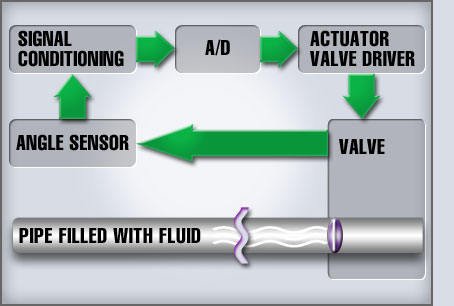 |
We need to start with an application, then determine the accuracy and precision that application requires as it relates to an angle/rotary-position sensor. Let’s consider an hydraulic valve operation for an actuator and say the valve moving up to 90° needs to be controlled within ±1.0°.
We need to create an error budget and assign maximum error amounts to each part
that affects the accuracy of moving the valve. The components involved are represented by the block diagram at left.
|
Each component in the application contributes to the error total including the fluid the valve is in contact with through its bulk modulus elasticity. However, closed-loop control can compensate for latent valve movement caused by fluid compression so, except for a small delay, we are left with adding up the tolerances of the angle sensor, signal conditioning circuitry, A/D converter, valve driver circuitry and hydraulic valve.
While we can add up the maximum tolerances of the components just mentioned, it will give a result that is a worst possible case. The worst case is unlikely, as all the errors from all the components would have to be operating at maximum error levels at the same time and in the same direction (positive versus negative error values). A more accurate way to calculate an error-budget is using the square root of the sum of the squares for each component, then add up the resulting errors. | READ ENTIRE ARTICLE INCLUDING EXAMPLE | |
|
|
 |
Wave Energy: Power Generation From Ocean Waves
It’s apparent to anyone who has seen large ocean waves cascading into a rocky coast or surfers riding them, that there is a great deal of energy in the waves of the sea. Harnessing those waves for power generation takes a great deal of engineering. The first to accomplish it with a commercial power plant is a company named Voith.
In northern Spain just outside a town called Motrico, Voith’s Hydro Wavegen Division built the power plant shown here (viewable on Bing Maps’ Bird’s Eye view too). It uses Nearshore Oscillating Water Column (OWC) technology. The structure houses 16 integrated Wells turbines that are located above a large chamber with an opening that is submerged under the water. As the ocean swell rises and falls so does the water level in the chamber. Rising water compresses the chamber air which is forced through the turbine generator. The falling water then sucks the air back through the turbine into the chamber. The Wells turbine is driven in the same direction irrespective of the air direction. The electricity generated is conditioned and exported to the grid enough to generate 300 kW of power to supply 250 homes.
One of the critical components in the plant is a Novotechnik RFC4800 touchless angle sensor. The sensor provides the position of a large butterfly damper used to isolate the turbines from the chamber during times of extremely rough seas or for shutdown purposes. The sensor is mounted on the turbine frame and its magnetic marker is affixed to the end of the actuator shaft. There are no bearings to wear and sensor and marker are sealed to IP69k for high reliability and long working life. Position of the damper is measured by the sensor to 0.09° and its analog output is absolute so there is no need to calibrate after a power shutdown.
"It’s a critical piece of equipment as the butterfly position is inherent to the safe operation of our turbine." Says Adam Young Wavegen's Business Development Engineer. "As you might imagine, given the conditions in which this equipment operates (salt laden air, cyclic positive and negative pressure) and in a commercial plant, it’s imperative that the equipment is robust and functions reliably."
|
|
 |